Introduction
Manufacturing is undergoing a technological revolution, driven by AI-powered tools that optimize processes, increase efficiency, and minimize costs. From predictive maintenance to automated quality control, AI in smart manufacturing enables industries to become more agile, scalable, and productive.
This step-by-step guide explores how to build AI tools for smart manufacturing, ensuring a SEO-optimized format that enhances search visibility and user engagement.
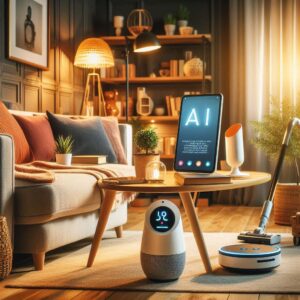
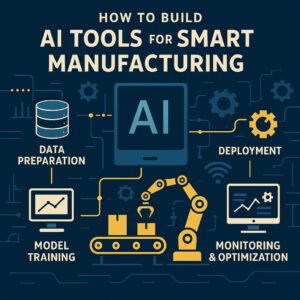
1. Why AI Tools are Essential for Smart Manufacturing
AI-driven solutions streamline manufacturing processes by leveraging real-time data, automation, and predictive analytics.
Key Benefits of AI in Manufacturing
- Predictive Maintenance: Identifies potential equipment failures before they happen, reducing downtime.
- Automated Quality Control: Uses computer vision and machine learning to detect defects and improve product consistency.
- Enhanced Supply Chain Management: Optimizes inventory levels, transportation logistics, and vendor operations.
- Smart Process Automation: Reduces manual intervention in repetitive tasks, increasing efficiency.
- Energy Optimization: AI monitors energy consumption, suggesting ways to minimize waste.
These benefits create a data-driven, responsive, and cost-effective manufacturing environment.
2. Technologies Behind AI Tools for Smart Manufacturing
Successful AI-powered manufacturing tools rely on integrating advanced technologies that analyze, predict, and automate industrial processes.
Core Technologies
- Machine Learning: Develops predictive models to improve manufacturing accuracy and efficiency.
- Computer Vision: Uses image recognition for quality inspection, defect detection, and process monitoring.
- Industrial Internet of Things (IIoT): Connects machines and devices, providing real-time production insights.
- Edge Computing: Processes data locally within manufacturing plants for faster decision-making.
- Cloud Computing: Offers scalable data storage and AI-driven analytics.
Integrating these technologies ensures seamless, intelligent automation across manufacturing operations.
3. Preparing Data for AI Models
AI thrives on structured, high-quality data to train machine learning models and enhance manufacturing efficiency.
Data Sources to Consider
- Sensor Data: Information from IIoT-enabled machines tracking temperature, vibration, and performance.
- Production Logs: Historical records of machine efficiency, downtime, and maintenance cycles.
- Quality Control Images: High-resolution pictures of defects used for training AI models in visual inspection.
- Supply Chain Data: Analytics on procurement, inventory management, and delivery schedules.
- Energy Usage Metrics: Historical power consumption data for optimization.
Steps to Process and Prepare Data
- Data Cleaning: Remove inconsistencies, duplicate records, and irrelevant entries.
- Feature Engineering: Highlight key variables such as pressure, cycle time, or sensor readings.
- Labeling for AI Models: Annotate defects, maintenance triggers, and process anomalies for model accuracy.
- Standardization: Convert data into structured formats compatible with AI systems.
High-quality data ensures precision, reliability, and adaptability in AI-powered manufacturing.
4. Training AI Models for Manufacturing Optimization
AI training enables smart systems to recognize patterns, predict failures, and automate decision-making.
Best Practices for AI Model Training
- Supervised Learning: Teach models using labeled manufacturing datasets for precise predictions.
- Unsupervised Learning: Discover unknown anomalies in production efficiency without predefined labels.
- Deep Learning Techniques: Apply neural networks for advanced image recognition and defect detection.
- Reinforcement Learning: Optimize AI performance by learning from real-time industry feedback.
- Hyperparameter Tuning: Adjust model settings for improved speed and accuracy.
Proper training transforms AI models into intelligent tools capable of real-time problem-solving in manufacturing.
5. Deployment Strategies for AI Manufacturing Tools
Seamless deployment ensures AI solutions integrate effectively into manufacturing environments.
Deployment Methods
- Edge Computing for Instant Processing: Deploy AI models on localized hardware for fast decision-making.
- Cloud-Based AI Platforms: Store and process vast data volumes for predictive insights.
- API Integrations: Connect AI models with existing manufacturing software systems.
- AI Dashboards for Visualization: Offer intuitive interfaces for production monitoring and analytics.
- Mobile & IoT Accessibility: Ensure AI tools can be accessed on mobile devices and IIoT-connected platforms.
Successful deployment ensures scalability, accessibility, and efficiency in smart manufacturing.
6. SEO Optimization for AI Manufacturing Tools
Building AI tools is only part of the process—SEO optimization ensures visibility among industry professionals and stakeholders.
SEO Best Practices
- Keyword Optimization: Use terms like “AI-powered smart manufacturing,” “industrial automation tools,” and “predictive maintenance AI.”
- Technical Content Marketing: Publish guides, tutorials, and case studies to establish authority in manufacturing AI solutions.
- Mobile-Friendly Website Design: Ensure fast loading speeds and seamless navigation across devices.
- Strategic Partnerships: Collaborate with manufacturing leaders and AI developers for thought leadership.
- Metadata Structuring: Use well-optimized page titles, descriptions, and alt tags for better ranking on search engines.
SEO strategies increase discoverability and position AI manufacturing tools as essential industry solutions.
7. Monitoring and Refining AI Systems for Long-Term Success
Regular updates and continuous monitoring maximize AI efficiency and adaptability in smart manufacturing.
Metrics to Track
- Accuracy of Predictions: Assess AI model performance in defect detection and predictive maintenance.
- Processing Speed: Measure AI response times for real-time manufacturing optimizations.
- User Adoption Rates: Track implementation success and employee engagement.
- Downtime Reduction: Evaluate decreases in unplanned maintenance and production halts.
- Data Security and Compliance: Ensure AI tools comply with industry regulations and cybersecurity protocols.
Continuous refinement ensures long-term optimization of AI-powered manufacturing tools.
Conclusion
AI tools for smart manufacturing are transforming industrial workflows, minimizing errors, and boosting efficiency. By integrating machine learning, IoT, and automation, manufacturers can optimize processes while cutting operational costs.